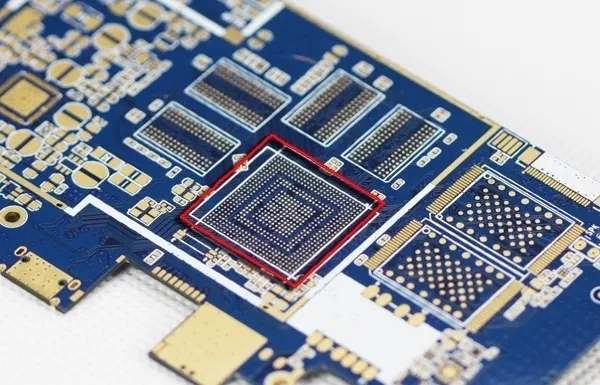
如何开始对产品的电子元件进行原型设计取决于您想要回答的问题。 每次创建新原型时,您都应该明确定义原型应回答的问题。 如果您对您的产品是否有效,或者是否能解决预期问题有广泛的疑问,您应该开始使用基于开发套件早期类似作品(例如 Arduino 或 Raspberry Pi)的原型。
如果您的产品功能没有大问题,您可能想直接设计定制PCB。 大多数开发产品的大公司都是从定制 PCB 开始的。 这是最快的上市方式,尽管它可能不是最便宜的。 定制PCB的原型设计包括两个步骤:制作裸PCB和焊接所有元件。 我们将分别讨论每个过程。
尽管有用于家庭生产的PCB技术,但它们仅限于简单的设计。 因此,您可能需要外包PCB原型生产。 假设您不制造和组装自己的 PCB,您将使用相同的流程来生产原型板并批量生产您的板。
PCB生产可概括为以下步骤:
该过程从由玻璃纤维环氧树脂制成的叠片铁芯开始。 它用作导电层之间的绝缘体,并为电路板提供物理强度。
单面板由叠片芯和一侧的铜层组成。 双面面板由每面都有铜层的叠片芯组成。 多层板由交替的铜层和叠片芯层组成。 大多数电路板将使用两个、四个、六个或八个导电层。
通过激光在薄膜上绘制每个导电铜层的布局设计,并应用光敏化学“抗蚀剂”。 然后将铜层暴露于穿透薄膜的高强度紫外线下。 该光使焊盘上的所有铜迹线和抗蚀剂层变硬。
然后用化学溶液处理铜层,以去除任何未被紫外线硬化的抗蚀剂层。 这仅在所需的铜迹线和焊盘上留下硬化的腐蚀抑制剂材料。 然后用另一种化学品去除未被抗蚀剂覆盖的任何暴露的铜。 然后去除硬化的抗蚀剂层,仅留下形成迹线和焊盘所需的铜。
接下来,使用层压工艺将所有层粘合在一起形成堆叠 PCB。
在 PCB 叠层上钻孔,形成通孔,用于连接不同层上的信号。 通孔组件中的所有孔也需要钻孔。 然而,通常最好仅使用表面贴装技术 (SMT) 组件,以最大限度地降低焊接成本。
然后,铜沉积在所有暴露的金属表面上,包括任何孔的内壁。 所有裸露的铜表面均镀有额外的铜。
现在裸PCB已经完成,下一步是放置和焊接所有电子元件。 机器人设备(称为拾取和贴装机)使用真空系统拾取元件并将其精确地放置在 PCB 上。 焊膏(焊料和助焊剂的粘性混合物)用于临时固定零件。
最后,电路板通过回流炉熔化焊膏,在元件和PCB焊盘之间形成永久的电气连接。 电路板组装和电路板加工制造商讲解电子硬件产品电路板设计和原型设计的基本准则。
工程样机
工程样机(有时也称为类似工程的外观样机)是第一次将外观与功能结合在样机中。 一旦你有了工程原型,你最终将拥有足够品质的东西来展示给客户和投资者。
现在是寻求外部投资者变得更加务实的时候了。 到此阶段,您已经克服了大部分工程和制造风险。 投资者显然喜欢这种风险降低。
对于我自己的硬件产品,现阶段的产品开发都是我自己出资的。 我用我的原型让一家大型全国零售商对我的产品感兴趣。 从那时起,我利用这一成功找到了愿意为剩余原型阶段提供资金的制造商。
工程原型接近批量生产原型,但尚未经过测试或准备批量生产。
预生产原型
这是外观相似的原型,已针对制造进行了优化。 这非常接近您的客户将看到的最终产品。 在大多数情况下,如果产品将通过零售店销售,则还应包括零售包装。
尽管预生产原型的外观和功能可能与类似作品非常相似,但关键的区别在于可制造性。 在产品开发过程中,许多企业家低估了从原型迁移到可高效制造的产品所需的工作量。 制造多个原型与制造数百万台有很大不同。 在大多数情况下,需要大量额外的设计工作来准备大规模制造的设计。
例如,在制作产品外壳原型时通常会使用3D打印或CNC加工。 对于大规模制造,将采用高压注射成型来生产外壳。
3D打印和CNC加工是非常宽容的技术。 您可以制作几乎任何可以想象到的塑料形状的原型。 注射成型则不是这种情况。 注塑成型有非常严格的生产要求。 完成3D打印原型后,需要进一步升级注塑设计。
注塑成型:3D打印非常适合生产数十个零件。 然而,生产数百个零件是不切实际的。 最后,注塑成型对于产品外壳的批量生产是必要的。 毫不奇怪,注塑工艺从模具的创建开始。 模具是由金属制成的,金属的硬度决定了模具的使用寿命和成本。
对于原型设计或早期生产,铝模具通常是最佳选择。 铝模具通常成本数千美元,最多可生产约 10000 个零件。 当热熔融塑料在高压下注入模具时,模具形成两半。 为了在零件中产生精细的细节,需要高压。 塑料冷却并固化后,打开模具并取出零件。
大多数设计都需要进行重大修改才能为注塑成型做好准备。 确保设计你的外壳的人了解注塑成型,否则你最终可能会得到一个可以是原型但无法批量生产的产品。 拥有一个功能齐全、工作正常、外观相似的原型机是一项伟大的成就,所以一旦你达到了这个里程碑,请拍拍自己的背!
但不要太兴奋......从原型到大规模制造的转变是将新硬件产品推向市场的最被低估的步骤之一。
工程验证测试(EVT)
完成项目原型后,您可以开始测试它以验证它是否完全按照指定方式工作。
该测试的第一阶段称为工程验证测试(EVT)。 此测试阶段重点关注电子产品。 EVT 期间通常会测试 10-50 台设备。 EVT将包括测试基本功能,同时也会进行各种压力测试,以确保不存在隐藏问题。 这包括功率、热和 EMI 测试。 EVT 的目标是验证您的原型是否满足功能、性能和可靠性规范。
设计验证测试(DVT)
设计验证测试 (DVT) 是最复杂的阶段之一。 目的是确保产品符合任何必要的外观和环境规范。 与EVT阶段相比,所需的单元数量要多得多,通常为50-200单元。 这些设备将接受非常严格的测试,包括跌落、防火和防水测试。 设计验证测试的主要目标之一是验证产品是否足够耐用以承受日常使用。 这通常也是获得电气认证的阶段。 这包括 FCC、CE、UL 和 RoHS 认证。
然后
联系
电话热线
13410863085Q Q
微信
- 邮箱