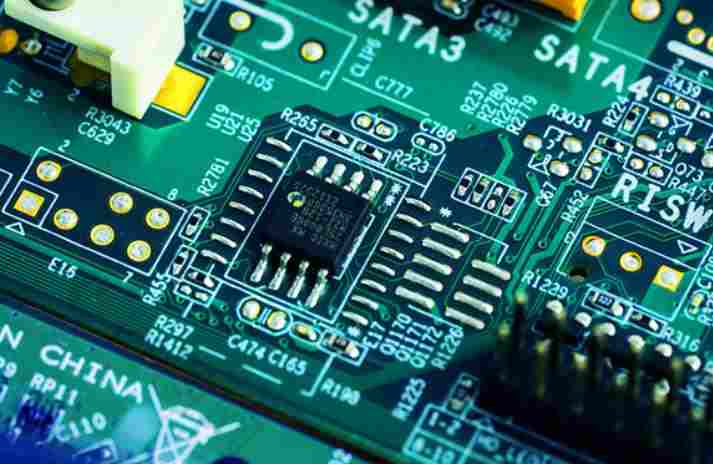
SMT贴片加工POP组装工艺介绍
芯片堆叠技术是现代电子信息产品为提高逻辑运算功能和存储空间而发展起来的一种新型高密度组装形式,本文主要从装备科学技术角度对POP组装工艺实现中存在的问题及对策进行分析和总结。 重点研究了POP组装工艺中主要工序工艺参数的优化方法和范围,讨论了工艺控制中需要注意的问题,这是保证POP芯片堆叠成功率的关键。
POP(Package on Package)是一种器件芯片堆叠技术。 它是为提高逻辑运算功能和存储空间而发展起来的一种器件小型化和高密度组装的新方法。
POP技术广泛应用于高端终端产品。 目前0.4mm间距的BGA POP技术已具备量产能力。
1、生产
目前0.4mm间距BGA POP组装工艺的主要难点是:
BGA印刷锡膏和0.4mm更低间距的回流焊易于桥接;
下两层放置精度高,移动方便;
难以控制上芯片的助焊剂浸渍量。
2、锡膏印刷
2.1 影响因素
印刷是一项系统工程。 PCB、模板、焊膏和设备在一定的环境下按照一定的方法协同工作,变量众多,相互作用机制复杂。 总结一下主要影响因素,
锡膏印刷的质量受硬件、工艺参数、环境和过程控制等因素的影响。 细间距元件可靠印刷的PCB及模具设计、锡膏选择、工艺控制等问题在很多文件中都有详细的分析和讨论,这里不再赘述。
2.2 支持方式
常见的配套套管有“硬”套管和“软”套管。
对于细间距元件的锡膏印刷,需要保证PCB与模具之间没有间隙,并且在整个印刷过程中PCB与模具平整且不变形。 通常认为顶针顶部越高,PCB与模具的连接越紧密,有助于提高印刷质量,这是错误的。 但如果套筒顶部太高,PCB和模具就会产生一定程度的预变形,如图4所示。一方面,模板开口与焊盘之间的对齐可能会发生偏移, 这可能会导致印刷锡膏移位; 另一方面,在刮刀移动过程中,模具与PCB会分离,导致不同区域获得的焊膏量不均匀,甚至焊膏量不足; 同时,在打印过程中分离模板时,分离速度和分离距离参数失去意义,容易锐化。
印刷支撑治具的引入,可以有效保证PCB与SMT模具的紧密结合,对0. 4mm/0.35mm间距、软/片变形等印刷问题改善明显。
2.3 刮刀
印刷过程中,焊膏应具有良好的滚动效果。 由于滚动,刮刀前端区域的锡膏会部分填充模板孔,其中的助焊剂会预先润湿模板孔壁,有利于后续锡膏的进一步填充和脱模,因此 以获得理想的焊膏数量和形状。 原来的“锡膏滚柱”直径约为15mm。 当缩小到原来尺寸的一半时,需要添加新的焊膏。 “锡膏滚柱”应均匀、光滑。
为了达到良好的滚压效果,除了保证锡膏适当的粘度和体积外,各个设备供应商都在寻求改进刮刀的结构和工作原理。 例如DEK的振动刮刀、ProFlow、Minami的旋转刮刀等。
2.4模具清洗频率
在丝网底部清洁的前提下,应尽量减少丝网的清洗频率。 采用切割方法加工的钢网壁上存在各种大小的毛刺,阻碍焊膏的填充和脱模。 在正常的印刷过程中,丝网壁会被助焊剂润湿,各种力会达到平衡状态。 在清洗过程中,由于酒精和真空的作用,助焊剂润湿的薄膜被破坏,毛刺再次暴露出来。 只有经过几个印刷周期后才能建立新的平衡。 这就是为什么在生产中清洗过的模具在第一次印刷时锡含量会下降的原因。
过于频繁的清洗还可能导致溶剂混入焊膏中,影响焊膏的粘度; 溶剂挥发会影响锡膏和模具的最佳工作温度,破坏系统平衡。
3、补丁
与传统元件相比,POP贴装的关键问题是实现和控制助焊剂(焊膏)的浸渍效果,保证BGA的贴装精度。
3.1 补丁模式
Fuji NXT/AIM设备具有三种POP放置模式:
吸收设备-图像识别-浸入助焊剂贴片;
μ吸收装置-图像识别-浸没通量-图像识别-贴片;
拿起设备--浸入助焊剂--图像识别--贴片;
进口阶段选择了两种助焊剂进行对比测试,即蓝色助焊剂和无色助焊剂;
设备浸入蓝色助焊剂后,无法进行图像识别,只能使用第一种贴片模式;
白色助焊剂不会影响图像识别。 可以使用第二或第三补丁模式;
推荐使用白光通量和第二贴片模式。
3.2 浸渍助焊剂(焊锡膏)
富士助焊剂单元可实现助焊剂(焊膏)的自动供给和厚度的自动控制。
然后
联系
电话热线
13410863085Q Q
微信
- 邮箱